Nachhaltigkeit in der Automobilwirtschaft?
Die Antriebsarten sind nur einer der Bereiche, in denen die Automobilwirtschaft mit Hochdruck die Ökologie-Wende umsetzt: Bio-Materialien, Kreislaufwirtschaft, Recycling – in den Produktions- und Lieferketten steckt mindestens ebenso viel Potential, wie in der Fahrzeugtechnik selbst. Die Vorbildwirkung zählt doppelt: Von den immensen Investitionen und dem konzentrierten Know-How werden künftig auch andere Branchen profitieren.
Die Ausschöpfung des Nachhaltigkeits-Potentials in der Produktion bis zurück in die Liefer- und Rohstoffkette ist heute für praktisch alle Hersteller ein Kernthema – im Mittelpunkt stehen dabei CO2-Einsparung und der Ersatz problematischer Werkstoffe.
Grundsätzlich wird dafür in vier Hauptbereichen gearbeitet: Der Umstellung auf erneuerbare Energiequellen, der Reduzierung von Komponenten, der Verwendung Biobasierender Materialien und der Intensivierung von Re-Use und Recycling. Um bis zu 80 Prozent weniger CO2 soll die Produktion eines Pkw bis 2030 gegenüber dem Wert von 2019 verursachen – in Zahlen wäre das ein Durchschnittswert von nur noch 1,5 Tonnen CO2 im Vergleich zu vormals sechs. Den größten Anteil daran liefert der Schwenk der Hochofenbefeuerung für die Stahlverhüttung von Kohle- oder Gasbetrieb zu mit Öko-Strom hergestelltem Wasserstoff, natürlich auch die Versorgung der Fabriken mit Strom aus erneuerbaren Quellen. In der Produktionslogistik trägt die sortenreine Trennung von Schnittmaterial in den Presswerken zur Nachhaltigkeit bei.
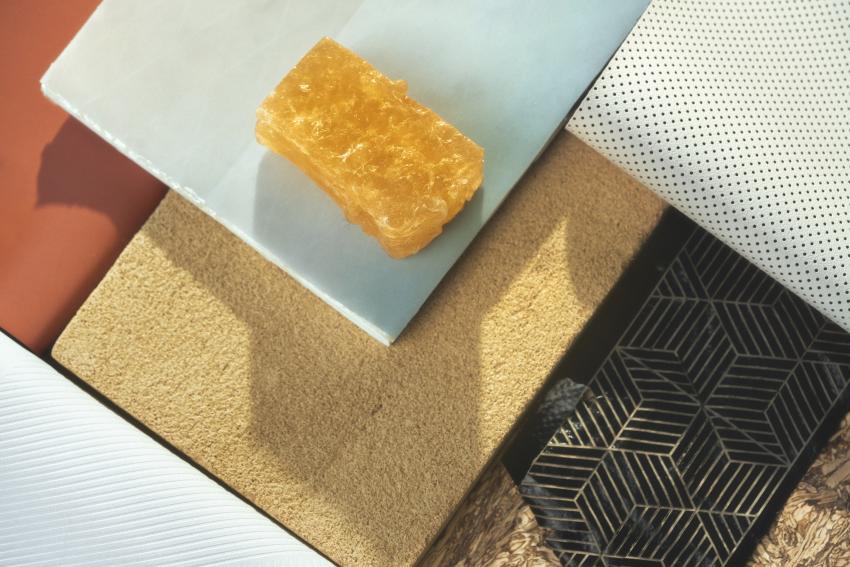
Verschiedenste Bio-basierende Materialien ersetzen bereits jetzt verstärkt Stoffe auf petrochemischer Basis. Vor allem Plfanzenfasern und Nebenprodukte der Nahrungsmittelherstellung kommen zum Einsatz.
Schlau trennen und einfach bauen
Bis vor kurzem wurden die unterschiedlichen Stahl- und Aluqualitäten, die dort zum Einsatz kommen, unsortiert gesammelt. Inzwischen gehen die einzelnen Materialarten getrennt zurück in die Neuverarbeitung, womit der Aufwand dort entsprechend sinkt. Nach Berechnungen einzelner Hersteller lässt sich mit der intensiven Nutzung von Recycling- und Sekundär-Material sowie der Umstellung der Energiequellen die Karosseriefertigung mit bis zu 83 Prozent CO2-Reduzierung betreiben.
Recycling beginnt nicht erst mit der Wiederverwertung, sondern bereits mit der Konzeption der Komponenten, die später einmal in diesen Kreislauf eintreten. Mono-Material kommt inzwischen verstärkt bei der Innenausstattung von Pkws aber auch äußeren Anbauteilen zum Einsatz. Etwa werden Stossfänger nicht mehr mit in den Kunststoff eingegossenen Metall-Teilen befestigt, sondern mit Clips, die aus demselben Plastik gefertigt sind, wie der Korpus selbst. Beim Recycling entfällt somit der aufwendige Arbeitsgang der Materialtrennung. Ähnlich ist die Handhabung bei Teppichen und Fußmatten: Obermaterial, Bordüre und die Naht haben zwar weiterhin unterschiedliches Aussehen und Haptik, werden aber aus einem Basismaterial gefertigt und daher im Recycling als Ganzes weiterverarbeitet.
Netzqualität und Faserschmeichler einmal anders
Mit einem direkten praktischen Nutzen verbunden ist die Verwendung von Nylon aus alten Fischernetzen. Mehrere Automobilproduzenten arbeiten mit Umweltschutzorganisationen zusammen, die diese die Meeresfauna und -flora beeinträchtigenden Netze aus dem Wasser bergen. Andere gehen noch einen Schritt weiter und kaufen Altbestände auf, bevor sie überhaupt im Meer entsorgt werden können. In jedem Fall werden daraus hochwertige Teppiche oder Sitzstoffe, denen das Vorleben ihres Basismaterials nicht anzumerken ist. Ebenfalls verbreitet ist mittlerweile der Einsatz von biobasierenden Materialien, etwa mit veganem Lederersatz, der auf Basis von Naturkautschuk, Mais oder Kaktus hergestellt wird. Den Vorreiter macht hier vielfach die Mode-Industrie – was bei Schuhen den Belastungs- und Haltbarkeitstest im Alltag besteht, kommt auch für Autointerieurs in Frage.
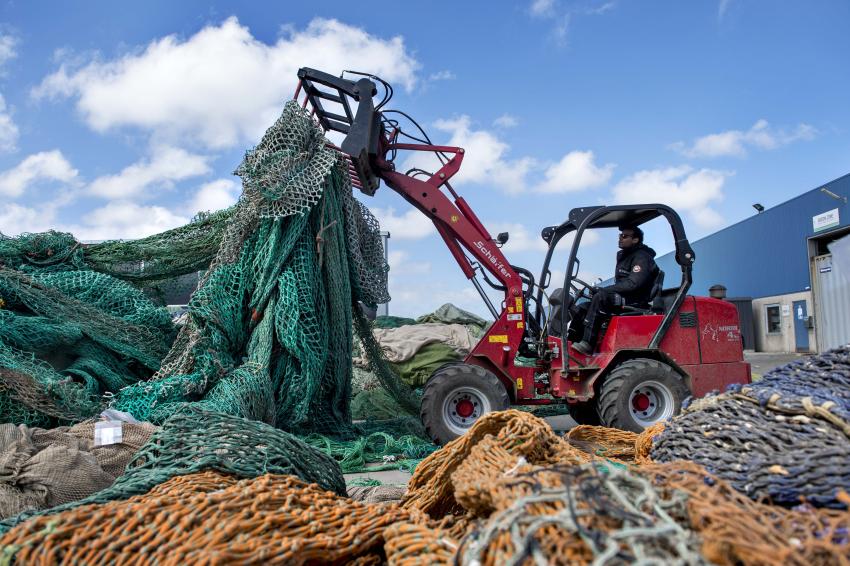
"Geisternetze", die herrenlos im Meer treiben, können großen Schaden anrichten – in nachhaltig gefertigten Autos wird daraus das Material für Teppiche oder Stoffe, denen niemand ihr Vorleben anmerken würde.
Ohne petrochemische Bestandteile, wie sie in herkömmlichem Kunstleder enthalten sind, lässt sich biobasierendes PVC mit rund 45 Prozent weniger CO2-Emissionen herstellen. Einer der vorbildlichsten Beiträge dazu trägt sogar ein rot-weiß-rotes Mascherl: Das Traditionsunternehmen Lenzing aus Oberösterreich liefert den Rohstoff für eines der aktuell haptisch ansprechendsten und durch seine atmungsaktiven Eigenschaften auch angenehmsten Sitzmaterialien auf dem Markt. Die Basis dafür: Zellstoff, mit Holz aus nachhaltiger heimischer Forstwirtschaft hergestellt.
Bio-Fasern stehen auch bereits in den Startlöchern, in der Kunststoff-Fertigung eine maßgebliche Rolle zu spielen. Flachs und Hanf bieten Festigkeit und Stabilität, dazu stammen sie aus europäischem Anbau und reduzieren damit Lieferabhängigkeit und Transportwege. Sie lassen sich zu weichen Obermaterialien verweben und je nach Faserlänge unter Temperatur zu Hartschalen pressen oder im Spritzguss-Verfahren verarbeiten. Sogar Carbon-Look kann so preisgünstig imitiert werden, dazu kommt eine Gewichtsersparnis von rund 20 Prozent gegenüber konventionellem Kunststoff.
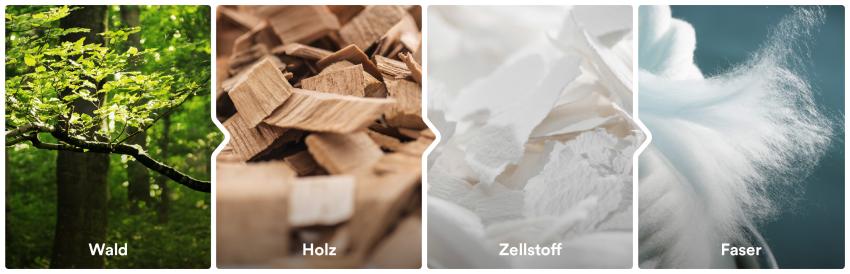
Made in Austria: Bei Lenzing in Oberösterreich wird Holz aus nachhaltiger Forstwirtschaft zum Rohmaterial für haptisch ansprechende und besonders atmungsaktive Sitzbezüge verarbeitet.
Engagement mit Breitenwirkung
Auch bei der Lieferung der fertigen Fahrzeuge werden neue Wege beschritten: Im kommenden Jahr sollen erstmals Lastensegler einen Teil der Transatlantik-Tranporte übernehmen. Die Neuorientierung der Produktion betrifft übrigens alle Modelle gleichwertig – egal, welchen Antrieb sie haben. Von der Investitionsstärke der Autobranche profitieren zudem andere Industriezweige, die das Kapital für derartige Umstellungen nicht aufbringen könnten, aber die neuen Produktionsmethoden künftig übernehmen werden. Der Anspruch der Automobilwirtschaft als Leitindustrie erneuert sich damit von selbst – sie darf sich jetzt auch zurecht als Nachhaltigkeits-Zugpferd bezeichnen.